Share
Pin
Tweet
Send
Share
Send

In one of the rooms there was clearly not enough light night lighting, so it was necessary to put some kind of simple lamp. I decided to make it with my own hands from wood, which will allow it to fit into the overall interior much better than using purchased plastic or metal nightlights. I will tell in more detail.
Materials used
For the manufacture of the lamp, I used almost the cheapest materials:
- rail 30x20 mm - 1.2 m;
- board 150x20 mm - 0.45 m;
- board 200x30 mm - 0.9 m;
- LED strip - 1.5 m;
- 1.5 kv copper stranded electrical cable mm - 2 m;
- terminal block;
- 12V power supply;
- small cloves;
- wood glue.
Production and assembly of LED lighting
First you need to make a light bulb template. It is drawn or printed on a sheet of A4 paper. Next, using a knife or scalpel, you need to cut it.

I dissolve the existing 200x30 mm board into 3 pieces 30 cm long. Alternately I attach a template to them and draw them around with a pencil. As you can see, at first I draw only the inside of the lamp.

Now I make a through hole on the inside of the circled workpiece, insert a jigsaw into it and cut along the contour. Since the width of the nail file does not allow turning at 90 degrees, then first make a rough cut and remove the excess, and then carefully cut under the line from the pencil. So prepare all 3 bulbs.

A jigsaw is an inaccurate tool, so the cut is rough. Having taken a rasp I bring the surface to an ideal.
I fasten the workpieces on the worktop of the workbench with screws so that they are firmly held during further processing with a power tool.
The cutters are mounted on a manual milling cutter to select a groove 10 mm wide. I set the depth of the upper groove processing line to 10 mm and go through the inner ends of the workpieces along the perimeter cut by a jigsaw. The result is a groove 10 mm wide and the same side walls.
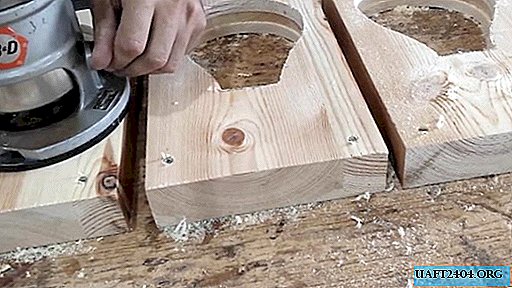
Next, I cut the paper template to the end and apply it to the processed workpiece. I outline the external dimensions of the bulb. The main thing here is to keep the paper tightly pressed so that it does not move, since in the future such an error will be noticeable on the finished part.

Now I trim the outside of the workpiece. This is convenient to do on a band saw, because it accurately maintains an angle of 90 degrees between the sides of the part. Of course, in its absence, you can act with a jigsaw.

Next, you need to process a rough cut from the saw. I make it a cylindrical grinding machine. A few passes are enough and the outside becomes smooth. Of course, the grinding cylinder is not a panacea, so I bring the angles in the lamp base part with an ordinary emery cloth mounted on a wooden block.



To fix the light bulb in the lamp and connect the electric wire to it, you need to drill a through hole on the end of the base. To do this, you can use an 8 mm drill. On the back of the hole, you need to countersink with a 10 mm drill. So we prepare all 3 blanks.

Now I am engaged in fixing the lamp. To do this, I remove the chamfer on the board 150x20 mm.
Next, I take a wooden lath and cut it into four pieces. Of these, 2 are 45 cm long and 2 are 15 cm long. Customizing their ends to 45 degrees. Next, I fold the frame out of them, previously smearing the ends with glue.

In order not to use clamps and not to wait, I additionally hammer small nails into the frame. I coat its lower part with glue, and glue it to the board with a chamfer, also reinforcing the structure with carnations.
As a result, I got a box. On the outside of its bottom, I drill 3 holes at the same distance from each other, indenting 4 cm from the edges.
I take a skein of LED strip, and I bring it into the groove of bulbs to measure the required circumference. Next, cut off 3 pieces of tape. I turn on the soldering iron and solder the wires on the tapes to connect to the power supply. The length of the wires for each workpiece is different. I use segments of 40, 50 and 60 cm.

Now I am tying a knot on the wire from the side of the LED strip and driving the free end through the hole in the lamp base. A bundle will not allow the wire to exit.
I tear off the protective film on the tape and glue it into the groove of the bulb. I do this on all workpieces.

Looking for some wires coming out of the bulbs into the holes of the box. At the inserted ends I also make knots so that the wires do not slip out. I connect the remaining small ends of the wires together in the terminal block. I fix it myself in the bottom of the box.


To the second part of the terminal block, I fix the cable coming from the 12V power supply. I put the block into the box, leaving only the output with the plug to be plugged in.


All the lamp is ready. I install it on the wall and turn it on. Since I am a professional carpenter, I have at my disposal a complete set of tools and equipment, which greatly simplified the manufacturing process. The whole charm of this lamp is that, if desired, it can even be done with only a hand jigsaw, knife, screwdriver with drills, a rasp, a short chisel, emery cloth, a plane and a hammer.


Share
Pin
Tweet
Send
Share
Send